HPPMS High Power Pulsed Magnetron Sputtering PVD Coating Technology
High Power Pulsed Magnetron Sputtering (HPPMS), also known as High Power Pulsed Magnetron Sputtering (HIPIMS) is a PVD coating technology based on magnetron sputtering deposition.HPPMS utilizes kW/cm 2The very high power densities of the order of magnitude are measured in short pulses (pulses) of tens of microseconds at low duty cycles (on/off time ratios) of less than 10%.The distinguishing feature of HPPMS is the high degree of ionization of the sputtered metal and the high dissociation rate of the molecular gases, which results in high densities of the deposited films. The degree of ionization and dissociation increases according to the peak cathode power. This limit is determined by the transition of the discharge from the glow to the arc phase. The peak power and duty cycle were chosen to maintain an average cathode power (1-10 W/cm) similar to conventional sputtering.
HPPMS is used for:
- Pre-treatment of substrates for adhesion enhancement prior to coating deposition (substrate etching)
- Deposition of coatings with high microstructural density
HPPMS uses a large energy pulse delivered to the cathode over a very short period of time (typically ~100 μs). This requires a very different type of power supply [1].The HPPMS process delivers a large low-energy ion flux to the substrate. The power supply must produce a peak power of up to 3 MW / pulse with a pulse width between 100 and 150 μs. The average power is about 20 kW at frequencies up to 500 Hz. in addition to providing the pulse power, arc suppression must be performed. The process takes advantage of the enhanced ionization produced by the high-energy pulses. The power density applied to the target is about 1 - 3 kW / cm 2(with a power density of about 1 - 10 W/cm) 2's(compared to conventional magnetron sputtering) [2].
Due to the enhanced ionization, HPPMS can be used to accomplish the growth of the crystal film as well as to control its phase composition [3]. Deposition conditions are equally important, but the duty cycle of the power supply and plasma parameters seem to contribute to the formation of the crystal structure. It was found that TiO 2of the rutile phase increases with pulse period and decreases with density with pulse amplitude [3]. However, other researchers have not seen this phenomenon and have only obtained amorphous films while depositing highly crystalline titanium [4].HPPMS has deposited highly crystalline ITO films.
As a result, HPPMS coatings should have improved tribological, optical, electrical and environmental properties. The improved microstructure also improves the optical properties [3,4,5-9]. It is well known that the refractive index depends on the density of the optical coating. The refractive index of less dense coatings is usually lower than that of more dense coatings.TiO 2Coatings are a perfect example of density-dependent materials. The refractive index of this material can vary between 2.2 - 2.5 depending on the density. Films deposited by HPPMS have been reported to have higher refractive indices compared to DC magnetron sputtered films as shown in Figure 1 [5]. The refractive index is higher over the entire spectrum. The density of these coatings is also 3.83 g / cm 3The density of the DC membrane was 3.71 g / cm 3, the surface roughness is 1.3 nm and the surface roughness is only 0.5 nm . If the optimal duty cycle of the power supply is used, the TiO 2 Coatingsalso has a high refractive index of about 2.72 [3]. Improvement of the refractive index of SiO 2ZnO, Al 2 o 3Ta 2 o 5and ZrO 2'sOptical performance movies have also been reported [6,7,8]. These results are impressive, but certain caveats must be noted. HPPMS coatings do not always have improved performance compared to coatings deposited using other power sources [10]. The optical constants are always highly dependent on the deposition conditions and the best set of conditions must be determined for each material and deposition system. I have seen very high refractive indices reported for planar magnetron sputtered films as well. In fact, in some cases, IF magnetron sputtering offers better performance than HPPMS [8].

Another advantage of the HPPMS process should be improved chemical and environmental stability. Silver coatings are notorious for their lack of chemical and environmental stability, especially very thin coatings. Although there are still many tests to be done, silver films deposited by HPPMS seem to have higher stability and optical properties in multilayer structures [9].
The process has the potential to improve the performance of friction coatings as density and smoothness increase [11-15]. Coatings with dense microstructures and smooth surfaces are preferred in many applications because they increase corrosion and wear resistance and reduce friction. Coatings such as TiN, CrN xCr x N yand Ti 3 SiC 2'sThe hard materials have been deposited by HPPMS. TiN coatings have a very fine grain structure compared to DC magnetron sputtering deposition [19].CrN coatings have even better microstructure than UBM sputtered coatings. Hardness values close to 25 GPa and a reduction in sliding wear coefficient from 7 to 0.2 have been reported [15].
HPePMS also deposited VMeCN and CrN / NbN friction superlattice coatings [16,17]. These structures show new high hardness values and low COF. the TiAlCN / VCN superlattice shows high hardness values (Hv = 2900 kg / mm 2) and a moderately low COF of 0.42. The CrN / NbN coatings show enhanced wear and corrosion protection as well as low surface roughness [16]. An important step in the process is the pretreatment of the substrate with V and Nb deposited by HPPMS.
Several resources state that HPPMS films should have low mechanical stresses [17]. Although stress measurements are inadequate, stresses in the vicinity of 3 GPa have been reported for CrN coatings [15].23 Stresses ranging from 1.6 GPa to 6.5 GPa have been measured in carbon films [18]. Low stresses have also been measured in TiN coatings [19,20].
HPPMS has been used to deposit low resistivity ITO films [21] and has shown promise for overall improvement in TCO performance.ZnO:Al films have also been deposited by this process. Almost all relevant reports have compared HPPMS coatings with DC magnetron sputtering coatings. Figure 2 compares the surface morphology of HPPMS and DC sputtered films deposited at 300 C [22]. Note again the very smooth surface of the HPPMS film. Figure 3 compares the resistivity films deposited by both methods (9a - DC and 9b - HPPMS). The resistivity achieved by the DC method in an o2The flow rate for 1sccm is ~3.2×10 -3 Ω.cm (the absolute state of ITO in this field), while the resistivity of the HPPMS method is 3.1 ~ × 10 -3 Ω.cm for the same O 2Flow. The authors concluded that this was a significant difference, with the lowest reported value for resistivity being 1.35 × 10 -3 Ω.cm dc film and ~1.25 X10 -3 Ω.cm for the HPPMS film.The real advantage of HPPMS seems to lie in the smoothness of the coating, and HPPMS won favor.
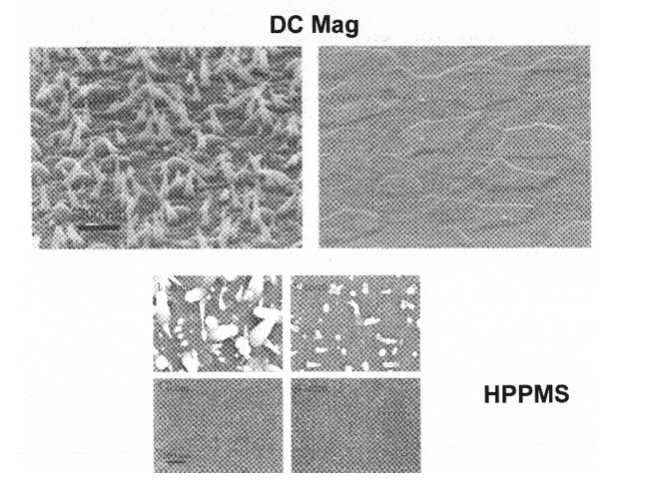

Go to http://vtcmagblog.com/
Reference:
- D J Christie et al., 47th Annual Technical Conference of the Society of Vacuum Coaters (2004) 113.
- William D. Sproul, 50 years of Vacuum Coating Technology and the growth of the Society of Vacuum Coaters, Donald M. Mattox and Vivienne Harwood Mattox ed. Society of Vacuum Coaters (2007) 35.
- R Bandorf et al., 50th Annual Technical Conference of the Society of Vacuum Coaters (2007) 160.
- J A Davis et al., 47th Annual Technical Conference of the Society of Vacuum Coaters (2004) 215.
- K Sarakinos et al., Rev. Adv. Mater. Sci, 15 (2007) 44.
- S Konstantinidis et al., 50th Annual Technical Conference of the Society of Vacuum Coaters (2007) 92.
- W.D. Sproul, D.J. Christie, and D.C. Carter, 47th Annual Technical Conference of the Society of Vacuum Coaters (2004) 96.
- D A Glocker et al, Proceedings of the 48th Technical Conference of the Society of Vacuum Coaters (2005) 53.
- J Li, S R Kirkpatrick and S L Rohde, Presentation SE-TuA1, AVS 2007 Fall Technical Conference, October 14 - 19, 2007, Seattle WA.
- D A Glocker et al., 47th Annual Technical Conference of the Society of Vacuum Coaters (2004) 183
- A P Ehiasarian et al., Proceedings of the 45th Technical Conference of the Society of Vacuum Coaters (2002) 328.
- J Böhlmark et al., Proceedings of the 49th Technical Conference of the Society of Vacuum Coaters (2006) 334.
- J Alami et al., Thin Solid Films 515 (4): 1731-1736.
- A P Ehiasarian et al., Surface and Coatings Technology 163-164: 267-272.
- J Paulitsch et al., Proceedings of the 50th Technical Conference of the Society of Vacuum Coaters (2007) 150.
- A P Ehiasarian et al, Proceedings of the 49th Technical Conference of the Society of Vacuum Coaters (2006) 349.
- W D Sproul, Proceedings of the 50th Technical Conference of the Society of Vacuum Coaters (2007) 591
- B M DeKoven et al. Proceedings of the 46th Technical Conference of the Society of Vacuum Coaters (2003) 158
- SE+PS-MoA1: R. Chistyakov, "Modulated Pulse Power Deposition ofNanometer-Scale Multilayered Coatings", presented at the 2008 AVS Fall Technical Conference, Seattle, WA, October 21, 2008.
- SE+PS-MoA3: A. Amassian et al., presented at the 2008 AVS Fall Technical Conference, Seattle, WA, October 21, 2008.
- P Eh Hovsepian et al., Proceedings of the 50th Technical Conference of the Society of Vacuum Coaters (2007) 602.
- V Sittinger et al., Proceedings of the 49th Technical Conference of the Society of Vacuum Coaters (2006) 343.