- PVD Coating-TiN-Titanium Nitride-Gold Color
- PVD Coating-TiCN-Titanium Nitride-Gray
- PVD Coating-TiAIN-Titanium Aluminum Nitride-Purple Black
- PVD Coating-CrN-Chromium Nitride-Silver Gray
- PVD Coating - AlCrN - Aluminum Chromium Nitride - Grayish Black
- PVD Coating-TiSiN-Titanium Silicon Nitride-Antique Bronze
- PVD-coated-DLC-diamond-like-black (colorful when thin)
- Naxi PVD Coating List Wizard
PVD coating, also known as vacuum coating, nano-coating, titanium plating, etc., is a generic term for vacuum physical deposition process. For different metal surface application scenarios, functional requirements, need to choose different elements of the type of PVD vacuum coating.
The same PVD coating type, due to the different types of arc source, lattice growth shape, film structure, target quality, as well as pre-treatment, temperature control, vacuum, etc., the final quality of the film will be very different.
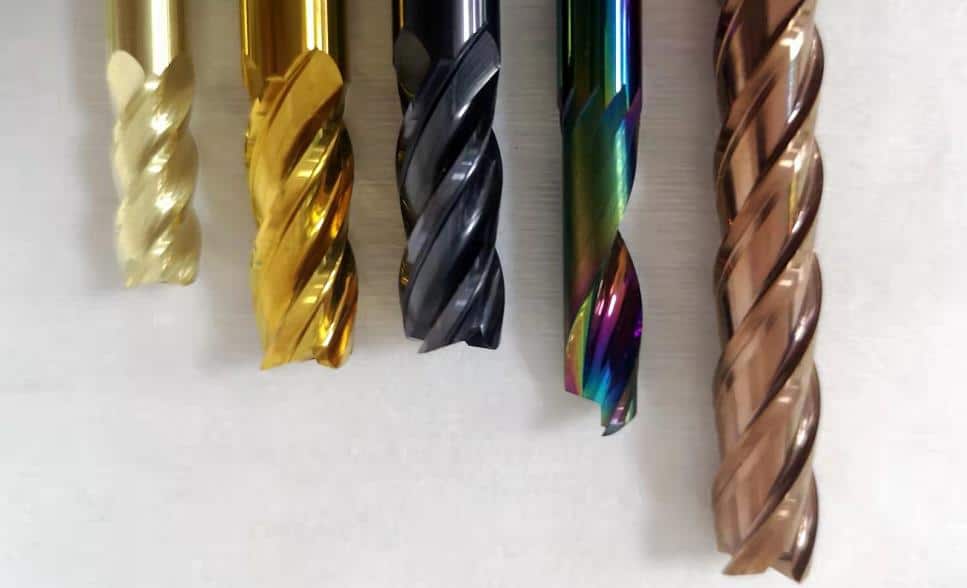
Nash common PVD milling cutter coatings
PVD Coating-TiN-Titanium Nitride-Gold Color #
Titanium nitride coating. It has 500°C oxidation resistance temperature, superior wear resistance, corrosion resistance.
It can be used not only for cutting tools, but also for knives, and can be widely used in molds, wire cutting machines, injection molded parts, etc.
PVD Coating-TiCN-Titanium Nitride-Gray #
Due to the influence of the carbon content, the advantages are high film hardness, good sliding properties. 450 ° C oxidation-resistant temperature, wear-resistant and anti-stainless steel adhesion.
Suitable for knives, punches, molds, pins, etc.
PVD Coating-TiAIN-Titanium Aluminum Nitride-Purple Black #
It has high temperature oxidation resistance due to the influence of aluminum content. 800°C oxidation resistance temperature, suitable for dry, high-speed cutting tools.
NanoShield Aluminum Titanium Nitride Tool Coating has a 4-layer SHRL coating system for excellent tool performance.
PVD Coating-CrN-Chromium Nitride-Silver Gray #
CrN (Chromium Nitride) coatings, which have an oxidation resistance temperature of about 600°C, are suitable for non-ferrous metals and polymers for anti-adhesion. For example, it is used for cutting tools made of copper materials, plastic injection molds.
PVD Coating - AlCrN - Aluminum Chromium Nitride - Grayish Black #
1100°C oxidation resistant temperature, the hardness of this coating does not drop at high temperatures, the coating performs best under severe temperature conditions such as dry gear cutting, aluminum die casting, etc., but the higher hardness is also suitable for deep drawing dies.
PVD Coating-TiSiN-Titanium Silicon Nitride-Antique Bronze #
With the addition of silicon base, the hardness of the coating and the hardness of the base layer are significantly increased, 1200°C oxidation resistance temperature. Enhances PVD coating hardness and abrasive wear while improving heat and corrosion resistance.
PVD-coated-DLC-diamond-like-black (colorful when thin) #
About 200℃ low temperature coating process, 0.1 low friction, 350℃ antioxidant temperature, film thickness 1-2μm, due to low surface roughness, it is difficult to adsorb lubricant. Suitable for precision transmission parts, aluminum alloys, thin plates, etc. requiring low temperature PVD coating process.
Conventional PVD vacuum coating, cavity temperature exceeds 500 degrees Celsius, coating time 0.5-1h, for 1mm within the plate coating, easily lead to substrate brittle, hardness reduction.