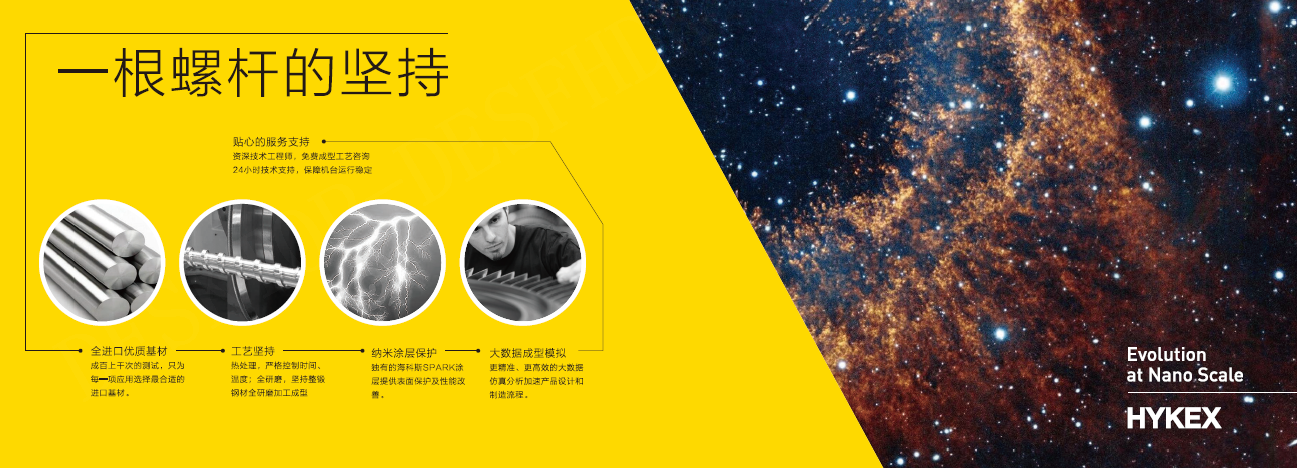
Whether the injection molding screw is electrochrome plated or PVD titanium plated should be considered according to specific application scenarios, performance requirements, cost considerations and environmental requirements. At present, injection molding screws are mainly used with electroplating process, while PVD technology is mainly used for injection molding high carbon fiber, glass fiber and other high hard wear-resistant materials.
Advantages and disadvantages of PVD titanium plating in injection molding screw applications: #
- Nasi PVD vacuum coating equipment with a maximum length of 1700mm; not suitable for large screws over 2 meters;
- PVD deposition temperature is high, the injection screw has the risk of deformation; PVD is usually deposited at high temperature of 300℃; usually higher stabilization corresponds to higher ion energy, better film quality and bonding force. Reasonable workpiece hangers, and precise temperature control, can maximize the guarantee of straightness;
- PVD titanium plating is 5-10 times higher in price compared with chromium plating. Especially in highly corrosive environments, the requirement of PVD layer to reach silk level thickness will increase the cost significantly; 1700 injection screws with PVD chromium nitride process are priced at more than a thousand dollars;
- PVD has very high requirements for pre-treatment, requiring the surface finish of the substrate to be Ra<0.2; the workpiece must be burr-free, oil-free and oxidized skin-free, etc.; unsuitable pre-treatment process will lead to coating shedding. Although it is possible to do fading treatment, but still need to increase the polishing to maintain the surface finish of the workpiece.
- PVD coatings are thin and cannot repair surface defects on the substrate as well as electroplating;
On the other hand, titanium plating is also widely used nowadays due to its process advantages such as high hard surface above 2000HV, denser coating structure, more choices of coating materials, higher temperature resistance, better bonding and more environmentally friendly. Especially, the latest high-power JVD technology developed by NANOX can realize fast and ultra-thick titanium plating, which significantly reduces the cost of coating and improves the life of injection molding screws at the same time.
Typical coating types for injection molding #
protective layer | Hardness: HV | Film thickness: μm | antioxidant temperature | coefficient of friction | Appearance Color | Suitable for processing materials |
CrN | 1800-2200 | 10-20 | 700 | 0.4 | ash gray | Applicable to transparent optical products, all kinds of lenses, light guide plate, etc.; commonly used plastics for optical products: PMMA, PC, COC, COP, CR-39, etc. |
CrAl+ | 3000-3500 | 5-7 | 1000 | 0.5 | dark gray | Glass fiber type, engineering plastics containing 70% or less; carbon fiber type, containing 50% or less; These plastics are PA, PC, PBT, PPS, PAR, PEI, PEEK, etc. |
DLC | 2000 | 1-3 | 350 | 0.1 | Black | Injection mold type; corrosion resistance, anti-adhesion; |
PVD Vacuum Coating Equipment #
- Magnetron sputtering equipment: denser film structure, better anti-adhesive effect;
- Arc ion plating: higher deposition temperature, harder coating structure, higher bonding and deposition rate; large surface droplets;