Tool Coating Passivation Value
Tool Coating Passivation Value
By deburring, smoothing and polishing the tool, the quality of the tool is significantly improved and its service life is extended.
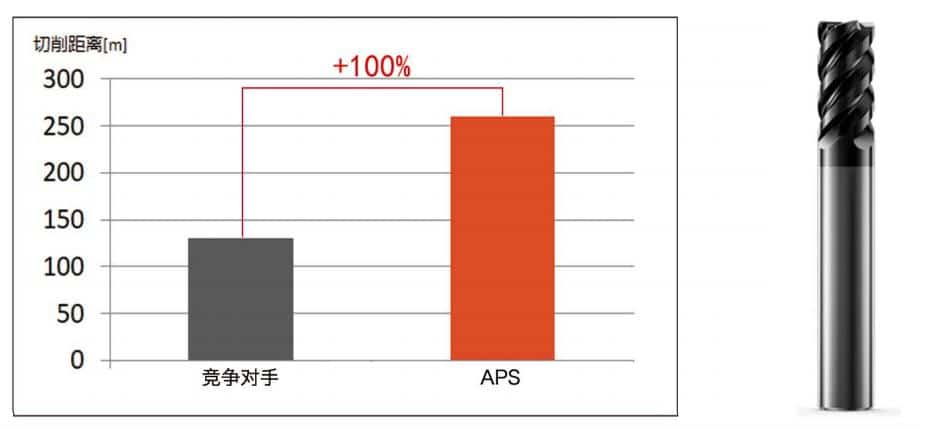
Superior tool coating solutions
1 Dramatically increase the strength and service life of the coating
After wheel grinding tool edge, there are different degrees of microscopic notch (i.e., tiny chipping and sawing). During the cutting process, the microscopic notches on the cutting edge of the tool are very easy to expand, accelerating tool wear and damage. Tool passivation treatment can effectively remove burrs and defects on the cutting edge, enhance the coating bonding force at the R corner, and thus improve the life of the tool.
2. Improvement of tooling speed and number of workpieces machined by polishing of grooves.
The coating front treatment polishes the tool recess uniformly, reduces its surface friction coefficient, effectively improves the sticky chip condition, and inhibits the formation of accumulated chip tumors. It also reduces the danger of biting between the tool and the machining material, reduces the cutting force of 40%, and makes the cutting smoother.
3 Formation of nanoscale depressions for improved tool machining speed and lifetime
The surface of the coated tool produces tiny protruding "droplets" that increase the surface roughness. After post passivation and polishing, the droplets are removed, leaving many small holes that can absorb cutting fluid during cutting, improving the lubricity and heat dissipation of the tool, thus increasing its machining speed and durability.
4 Reduces the stress on the du-coated layer and improves the sliding and coating bonding on the tool surface.
Traditional sand blasting can cause stripping of hard coating films such as DLC, chrome plating, etc.; Naxion's droplet removal polishing process can effectively adjust the coating stress and improve the coating quality.
Passivation technology for gas-fluid tools
1 Technical characterization
NanoShield's gas-fluid passivation technology can be tailored to meet the different needs of materials with different hardnesses, machining profiles, mirror surface requirements and other differentiated needs.
2 Aerofluidic grinding and polishing method
Principles of Aerofluidic Polishing Technology:
The use of high-density soft synthetic materials, made of soft polishing media (soft abrasives), accelerated by airflow, the horizontal elongation of the soft abrasive force so that it is easier to obtain sliding friction in the direction of Vx, and deformation to obtain the friction iteration, to obtain the polished distance s; the elastic properties of the soft substrate, as shown in the figure below, can be obtained with a very small amount of polished pressure P, and the contact pressure is uniformly distributed, which makes it possible to remove the extremely small amount Dp, which can be adjusted to the angle of incidence and speed, without any external lubrication. The elasticity of the soft substrate, as shown in the figure below, allows a very small polishing pressure P, and a uniform contact pressure distribution, which makes it possible to remove the extremely small amount of Dp by plastic deformation.
The sliding scratches of the abrasive grains and the very low polishing pressure obtained by this technology are the essential difference from the traditional dry and wet blasting methods.
Tool passivation applications
- All kinds of metal, ceramic, graphite molds, punches, guide pillars, slide rails, polishing of complex parts.
- Tool and cutlery edge burr removal, edge sharpening, and service life enhancement.
- Removes tool coating droplets, relieves stress, and reduces friction and wear.
- Remove grinding surface defects or oxidized layer, and improve coating adhesion for all types of tools.
- Other types of parts or products that need to be polished with functional or appearance requirements.
- Medical, Pharmaceutical.