HPPMS 고출력 펄스 마그네트론 스퍼터링 PVD 코팅 기술
고출력 펄스 마그네트론 스퍼터링(HPPMS)은 고출력 펄스 마그네트론 스퍼터링(HIPIMS)이라고도 하며 마그네트론 스퍼터링 증착을 기반으로 하는 PVD 코팅 기술로, HPPMS는 kW/cm를 활용합니다. 2매우 높은 전력 밀도는 10% 미만의 낮은 듀티 사이클(온/오프 시간 비율)에서 수십 마이크로초의 짧은 펄스(펄스)로 측정되며, HPPMS의 특징은 스퍼터링된 금속의 높은 이온화 정도와 분자 가스의 높은 해리율로 인해 증착된 필름의 밀도가 높다는 점입니다. 이온화 및 해리 정도는 피크 음극 전력에 따라 증가합니다. 이 한계는 글로우에서 아크 단계로의 방전 전이에 의해 결정됩니다. 피크 전력 및 듀티 사이클은 기존 스퍼터링과 유사한 평균 음극 전력(1-10W/cm)을 유지하기 위해 선택되었습니다.
HPPMS는 다음과 같은 용도로 사용됩니다:
- 코팅 증착 전 접착력 향상을 위한 기판 전처리(기판 에칭)
- 미세 구조 밀도가 높은 코팅 증착
HPPMS는 매우 짧은 시간(일반적으로 ~100μs)에 걸쳐 음극에 전달되는 큰 에너지 펄스를 사용합니다. 이를 위해서는 매우 다른 유형의 전원 공급 장치가 필요합니다[1]. HPPMS 공정은 기판에 큰 저에너지 이온 플럭스를 전달합니다. 전원 공급 장치는 펄스 폭이 100~150μs인 최대 3㎿/펄스의 피크 전력을 생산해야 합니다. 평균 전력은 최대 500Hz 주파수에서 약 20kW이며 펄스 전력을 제공하는 것 외에도 아크 억제를 수행해야 합니다. 이 공정은 고에너지 펄스에 의해 생성되는 향상된 이온화를 활용합니다. 대상에 적용되는 전력 밀도는 약 1 - 3kW / cm입니다. 2(약 1~10W/cm의 전력 밀도) 2's(기존 마그네트론 스퍼터링과 비교)[2].
강화된 이온화로 인해 HPPMS는 결정막의 성장을 달성하고 상 구성을 제어하는 데 사용할 수 있습니다 [3]. 증착 조건도 중요하지만 전원 공급 장치의 듀티 사이클과 플라즈마 파라미터가 결정 구조 형성에 기여하는 것으로 보입니다. TiO 2의 루틸 상은 펄스 주기에 따라 증가하고 펄스 진폭에 따라 밀도가 감소합니다 [3]. 그러나 다른 연구자들은 이 현상을 보지 못하고 고결정성 티타늄을 증착하면서 비정질 필름만 얻었습니다[4].HPPMS는 고결정성 ITO 필름을 증착했습니다.
결과적으로 HPPMS 코팅은 마찰, 광학, 전기 및 환경 특성이 개선되어야 합니다. 개선된 미세 구조는 광학적 특성도 개선합니다[3,4,5-9]. 굴절률은 광학 코팅의 밀도에 따라 달라진다는 것은 잘 알려져 있습니다. 밀도가 낮은 코팅의 굴절률은 일반적으로 밀도가 높은 코팅의 굴절률보다 낮습니다.TiO 2코팅은 밀도 의존적인 재료의 완벽한 예입니다. 이 물질의 굴절률은 밀도에 따라 2.2 - 2.5 사이에서 달라질 수 있습니다. 그림 1 [5]에서 볼 수 있듯이 HPPMS로 증착된 필름은 DC 마그네트론 스퍼터링 필름에 비해 굴절률이 더 높은 것으로 보고되었습니다. 굴절률은 전체 스펙트럼에 걸쳐 더 높습니다. 이 코팅의 밀도 또한 3.83g/cm입니다. 3DC 필름의 밀도는 3.71g/cm였습니다. 3의 표면 거칠기는 1.3nm, 표면 조도는 0.5nm에 불과합니다. 전원 공급 장치의 최적 듀티 사이클을 사용하는 경우, TiO 2 코팅는 약 2.72의 높은 굴절률을 가지고 있습니다[3]. SiO의 굴절률 개선 2ZnO, Al 2 O 3Ta 2 O 5및 ZrO 2's광학 성능 필름도 보고되었습니다[6,7,8]. 이러한 결과는 인상적이지만 몇 가지 주의해야 할 점이 있습니다. HPPMS 코팅은 다른 전원으로 증착한 코팅에 비해 항상 향상된 특성을 갖는 것은 아닙니다[10]. 광학 상수는 항상 증착 조건에 따라 크게 달라지며 각 재료와 증착 시스템에 맞는 최적의 조건 세트를 결정해야 합니다. 평면 마그네트론 스퍼터링 필름에 대해서도 매우 높은 굴절률이 보고된 바 있습니다. 실제로 어떤 경우에는 IF 마그네트론 스퍼터링이 HPPMS보다 더 나은 성능을 제공하기도 합니다[8].

HPPMS 공정의 또 다른 장점은 화학적 및 환경적 안정성이 향상된다는 점입니다. 은 코팅은 특히 매우 얇은 코팅의 경우 화학적 및 환경적 안정성이 부족한 것으로 악명이 높습니다. 아직 많은 테스트가 필요하지만, HPPMS로 증착된 은막은 다층 구조에서 안정성과 광학적 특성이 더 높은 것으로 보입니다[9].
이 공정은 밀도와 부드러움이 증가함에 따라 마찰 코팅의 성능을 향상시킬 수 있는 잠재력을 가지고 있습니다[11-15]. 조밀한 미세 구조와 매끄러운 표면을 가진 코팅은 내식성과 내마모성을 높이고 마찰을 감소시키기 때문에 많은 응용 분야에서 선호됩니다. TiN, CrN과 같은 코팅 xCr x N y및 Ti 3 SiC 2's경질 재료는 HPPMS로 증착되었습니다. TiN 코팅은 DC 마그네트론 스퍼터링 증착에 비해 매우 미세한 입자 구조를 가지고 있으며[19], CrN 코팅은 UBM 스퍼터링 코팅보다 미세 구조가 훨씬 더 우수합니다. 25 GPa에 가까운 경도 값과 슬라이딩 마모 계수가 7에서 0.2로 감소한 것으로 보고되었습니다 [15].
HPePMS는 또한 VMeCN 및 CrN/NbN 마찰 초격자 코팅을 증착했습니다[16,17]. 이러한 구조는 새로운 높은 경도 값과 낮은 COF를 보여줍니다. TiAlCN / VCN 초격자는 높은 경도 값 (Hv = 2900 kg / mm 2) 및 0.42의 적당히 낮은 COF를 제공합니다. CrN/NbN 코팅은 향상된 마모 및 부식 방지 기능과 낮은 표면 거칠기를 보여줍니다 [16]. 이 공정에서 중요한 단계는 HPPMS로 증착된 V와 Nb로 기판을 전처리하는 것입니다.
여러 자료에 따르면 HPPMS 필름은 기계적 응력이 낮아야 한다고 명시되어 있습니다[17]. 응력 측정이 불충분하지만, CrN 코팅의 경우 3 GPa 부근의 응력이 보고되었습니다[15].23 탄소 필름에서는 1.6 GPa에서 6.5 GPa 범위의 응력이 측정되었습니다[18]. TiN 코팅에서도 낮은 응력이 측정되었습니다[19,20].
HPPMS는 저저항 ITO 필름 증착에 사용되어 왔으며[21] TCO 성능의 전반적인 개선 가능성을 보여주었고, 이 공정을 통해 ZnO:Al 필름도 증착되었습니다. 거의 모든 관련 보고서에서 HPPMS 코팅과 DC 마그네트론 스퍼터링 코팅을 비교했습니다. 그림 2는 300°C에서 증착된 HPPMS와 DC 스퍼터링 필름의 표면 형태를 비교한 것입니다[22]. HPPMS 필름의 매우 매끄러운 표면에 다시 한 번 주목하세요. 그림 3은 두 가지 방법으로 증착된 저항률 필름을 비교한 것입니다(9a - DC 및 9b - HPPMS). DC 방법으로 달성한 저항률은 o21sccm의 유량은 ~3.2×10입니다. -3 Ω.cm(이 분야에서 ITO의 절대 상태)인 반면, HPPMS 방식의 저항률은 3.1 ~ × 10입니다. -3 동일한 O의 경우 Ω.cm 2흐름. 저자는 저항률에 대해 보고된 가장 낮은 값이 1.35 x 10인 점을 고려할 때 이는 상당한 차이라고 생각합니다. -3 Ω.cm DC 필름 및 ~1.25 X10 -3 HPPMS 필름의 경우 Ω.cm.HPPMS의 진정한 장점은 코팅의 부드러움에 있는 것 같으며 HPPMS가 유리합니다.
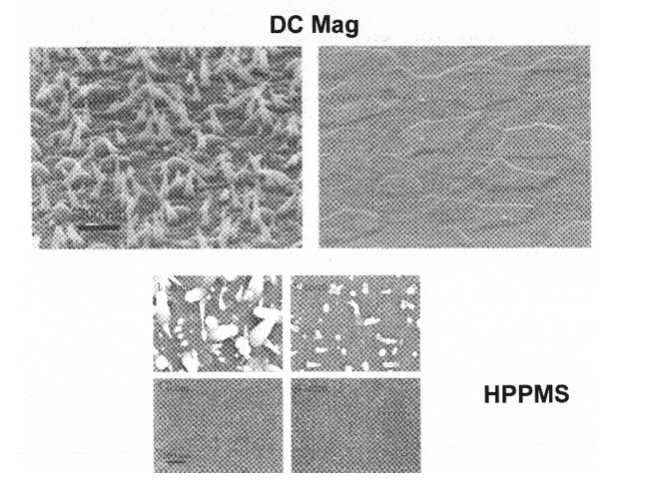

http://vtcmagblog.com/ 으로 이동
참조:
- D J Christie 외, 제47회 진공 코팅기 학회 연례 기술 컨퍼런스 (2004) 113.
- 윌리엄 D. 스프롤, 진공 코팅 기술의 50년과 진공 코팅 학회의 성장, Donald M. Mattox 및 Vivienne Harwood Mattox ed. 진공 코팅 학회 (2007) 35.
- R Bandorf 외, 제50차 진공 코팅기 학회 연례 기술 컨퍼런스 (2007) 160.
- J A 데이비스 외, 제47회 진공 코팅기 학회 연례 기술 컨퍼런스 (2004) 215.
- K Sarakinos 외, Rev. Adv. Mater. Sci, 15 (2007) 44.
- S 콘스탄티니디스 외, 제50차 진공 코팅기 학회 연례 기술 컨퍼런스 (2007) 92.
- W.D. Sproul, D.J. Christie, D.C. Carter, 제47회 진공 코팅기 학회 연례 기술 컨퍼런스(2004) 96.
- D A Glocker 외, 제48회 진공 코팅기 학회 기술 회의록 (2005) 53.
- J Li, S R Kirkpatrick 및 S L Rohde, 프레젠테이션 SE-TuA1, AVS 2007 추계 기술 컨퍼런스, 2007년 10월 14~19일, 워싱턴 주 시애틀.
- 진공 코팅기 학회 47차 연례 기술 컨퍼런스 (2004) 183
- A P Ehiasarian 외, 제45회 진공 코팅기 학회 기술 컨퍼런스(2002) 328쪽.
- J Böhlmark 외, 제49회 진공 코팅기 학회 기술 컨퍼런스(2006) 334쪽.
- J Alami 외, 얇은 고체 필름 515 (4): 1731-1736.
- A P Ehiasarian 외, 표면 및 코팅 기술 163-164: 267-272.
- J Paulitsch 외, 제50회 진공 코팅기 학회 기술 컨퍼런스(2007) 150.
- A P Ehiasarian 외, 제49회 진공 코팅기 학회 기술 컨퍼런스(2006) 349쪽.
- W D Sproul, 진공 코팅기 학회 제50차 기술 회의록(2007) 591쪽
- 진공 코팅기 학회 제46회 기술 컨퍼런스 (2003) 158
- SE+PS-MoA1: R. 치스티야코프, "나노미터 규모의 다층 코팅의 변조 펄스 전력 증착", 발표 내용 2008년 10월 21일, 워싱턴 주 시애틀, 2008 AVS 가을 기술 컨퍼런스.
- SE+PS-MoA3: A. Amassian 외, 2008년 10월 21일, 워싱턴주 시애틀, 2008 AVS 추계 기술 컨퍼런스에서 발표.
- 진공 코팅기 학회 제50회 기술 컨퍼런스(2007) 602쪽, P Eh Hovsepian 외, 진공 코팅기 학회 제50회 기술 컨퍼런스 논문집.
- V Sittinger 외, 제49회 진공 코팅기 학회 기술 컨퍼런스(2006) 343쪽.